Working with large assemblies: best practices
When creating an Illustrated Parts Catalog for large complex assemblies, it is not recommended that a single Cortona3D Item (project) is used. This may result in the following issues:
- A single parts list containing thousands of parts is too complex for the end-user to follow.
- The file size of the published parts catalog may cause long loading times or may be too large for web delivery.
- Due to the complexity and size of the assembly, the end-user and author may experience performance issues.
The assembly should be broken down into smaller subassemblies according to some logical grouping, e.g. function system, location, etc.
These projects are combined in a document structure to produce the full spare parts catalog. A project is created showing a high-level view of the assembly. This top-level view contains simplified versions of the major components of subassemblies. References are included at this level to the detailed Cortona3D projects (e.g. “See Oil system for Details”).
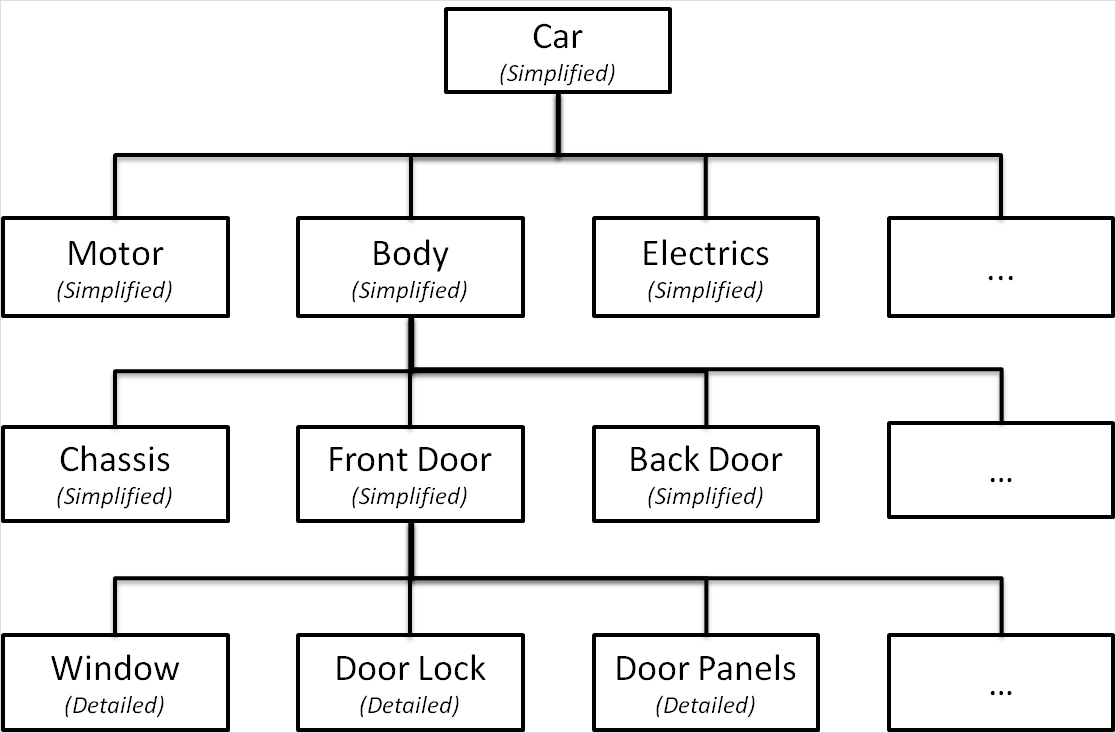
In the figure above we can see how a car could be broken down into multiple Cortona3D projects. The top-level is a high-level view of the car, showing simplified models of the major systems. References to each of these systems are included in this project.
In the level below, the Body project contains another simplified model. These models may include more details when compared to the model used in the level above. References are included for each of its major components.
The document can contain as many of these simplified projects as required until the subassemblies cannot be broken down further. A detailed project is then created for this level.
This provides the user with a logical way they can drill down through the assembly to find the components required. It also prevents the loading of unnecessary components that are of no interest to the user.
- Smaller parts lists are easier for the end-user to comprehend.
- The smaller output file size decreases loading times and improves performance.
- Multiple authors can work on different projects, reducing the amount of time required to author the content.
- Common elements can be reused across multiple Parts Catalog documents. For example, the Oil filtering system may be used on several models.
- Delete hidden parts
- Some components may be internal parts and are not visible to the end-user. Deleting these parts will not visibly impact the view that the user has, but will reduce the file size and complexity.
- Simplify the background parts
- Not all components of the assembly may be required for the document. These background parts are included as a navigation reference and can be simplified in RapidAuthor by deleting shapes and merging assemblies (details can be found in section 3.12 of Creating_3D_IPC.pdf in the products documentation).
- Create a simplified lightweight version of the product
- In some cases, the user needs to see where the subassembly fits in the overall assembly. The full assembly does not need to be seen in full detail – a simplified version is sufficient and has a file size significantly less than using the CAD models. This simplified version should be modeled on the same coordinate system as the CAD. This allows the author to only import the data that detail is required with the parts appearing in the correct locations on the simplified model.
Please see this article for Cortona3D RapidAuthor project data restrictions.